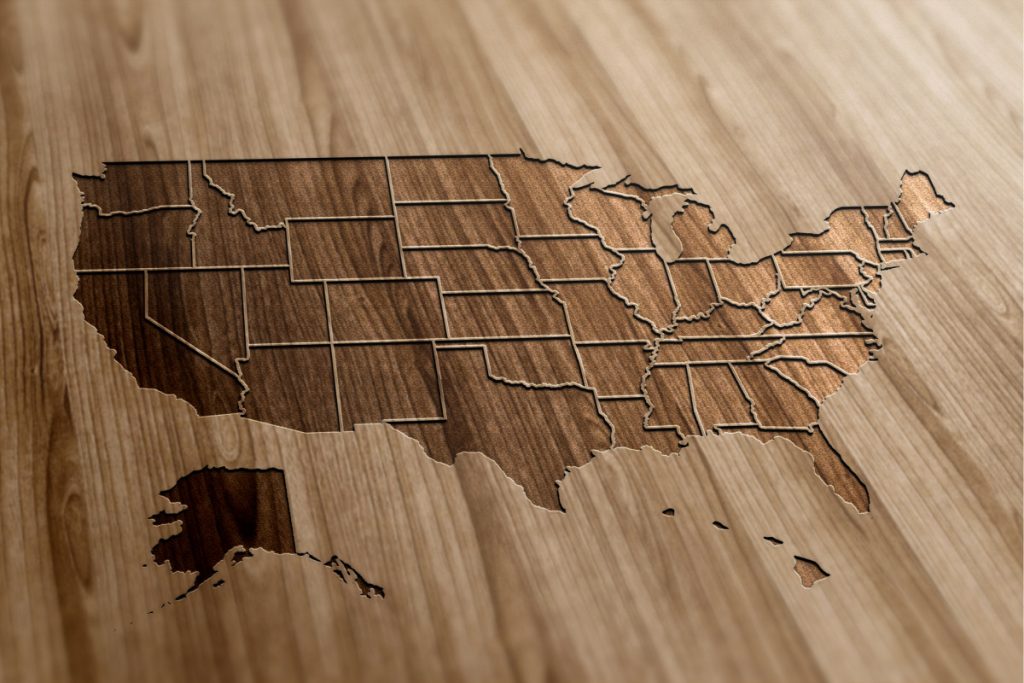
It can be challenging to transport rough lumber by hand. Take your handsaw and tape measure along with you to the shop. Additional boards can be purchased in case the one you have bought doesn't fit. You should also ensure that the board has checks and knots. They may not be as easy to plane down as you expected. You don't want to have to rip a board and start all over. It's a waste of time and money to do this, so you can buy one or two additional boards.
You save more
A sawmill turns roughly 59% of the rough lumber into boards. The rest of the log is made up of sawdust and bark. The log should be cut to a smaller size, but not more than 20%. Here is a simple formula that will estimate how much wood has been wasted in a given board. A 4-foot nominal board should be removed by the sawmill to reach the desired lumber thickness.
One thing is that rough lumber does not come in the same dimensions. The dimensions of hardwood bought from a big box store are often known, allowing you to plan your project around the standard size. It is possible for rough lumber to have uneven edges, leading to waste. The common width of rough-cut lumber can lead to a lot waste. These wastes can't be recycled later.
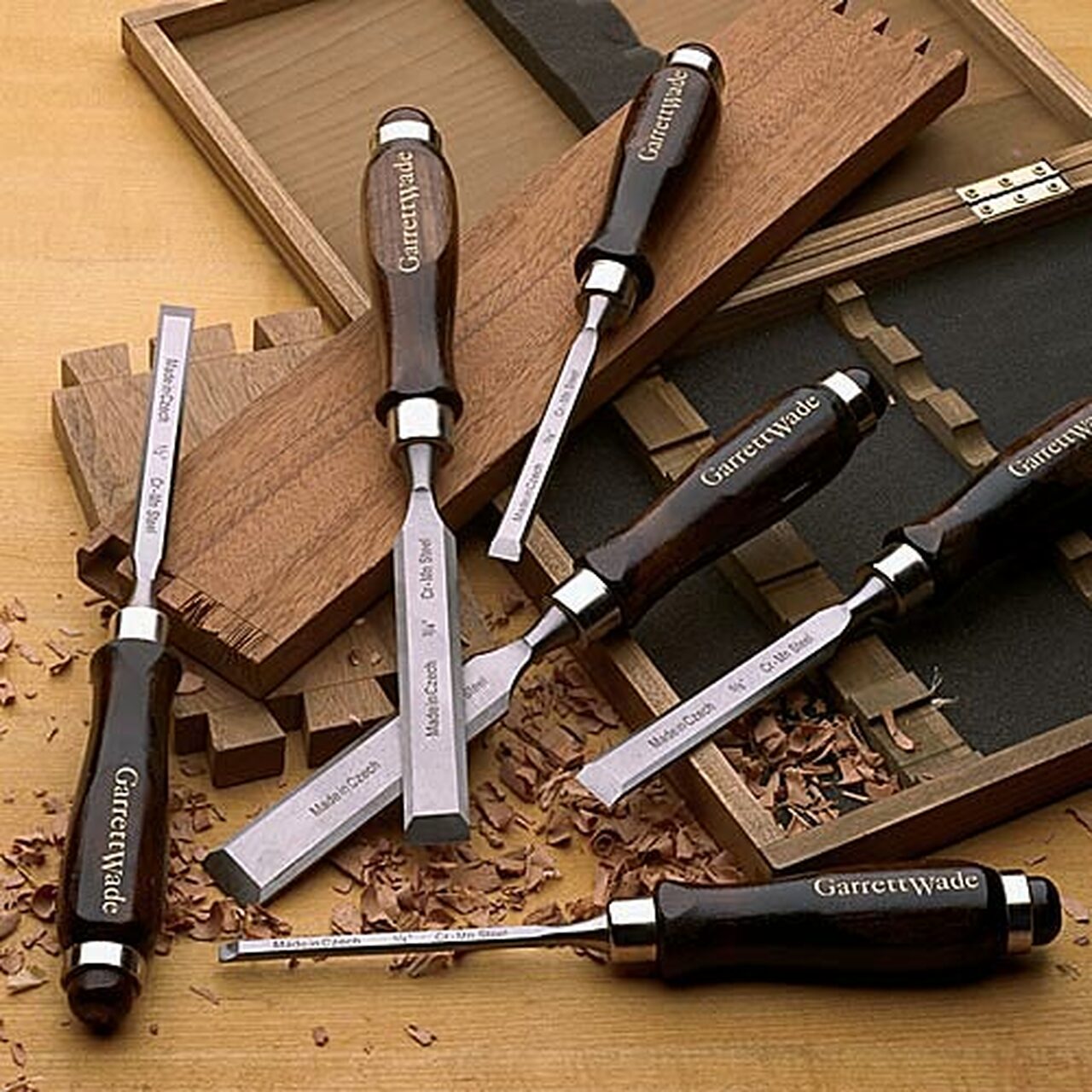
Preparation
The first step in preparing for cutting rough lumber is to measure the length of the material. Rough lumber may not arrive at the lumber yard perfectly flat. It might not have parallel faces or edges and may require multiple passes to flatten. The rule of thumb is 1/16" per pass. If the lumber has concave surfaces, run it through the saw with the concave surface down.
Generally speaking, rough cut lumber should be flattened to about 1/4" thick before the saw cuts it. After flattening, plane the face to the thickness you want for the finished board. Once you have measured and weighed the rough lumber, measure its length. You should account for any imperfections. Plan your project around the boards available. Make sure the lumber you buy is flat enough, as rough boards that are warped, bowed, or twisted are difficult to work with.
Cost
There are two types, dimensional lumber and rough sawn lumber. Home improvement stores generally carry finished lumber but very rarely rough-sawn. Both types are available in lumber yards and local sawmills. The main difference is in how much work they need to be processed. A rough-sawn board can be cheaper because it requires less processing. It is also more flexible than finished lumber in that it can be cut wider and thinner.
A lumber yard or mill will generally sell lumber at a lower price, but they are less likely to have standard lengths. Making your own lumber can save you money over buying rough-sawn lumber. However it will require some space and additional power. Milling equipment can be noisy and requires training. Consider the local zoning laws if you intend to use your mill.
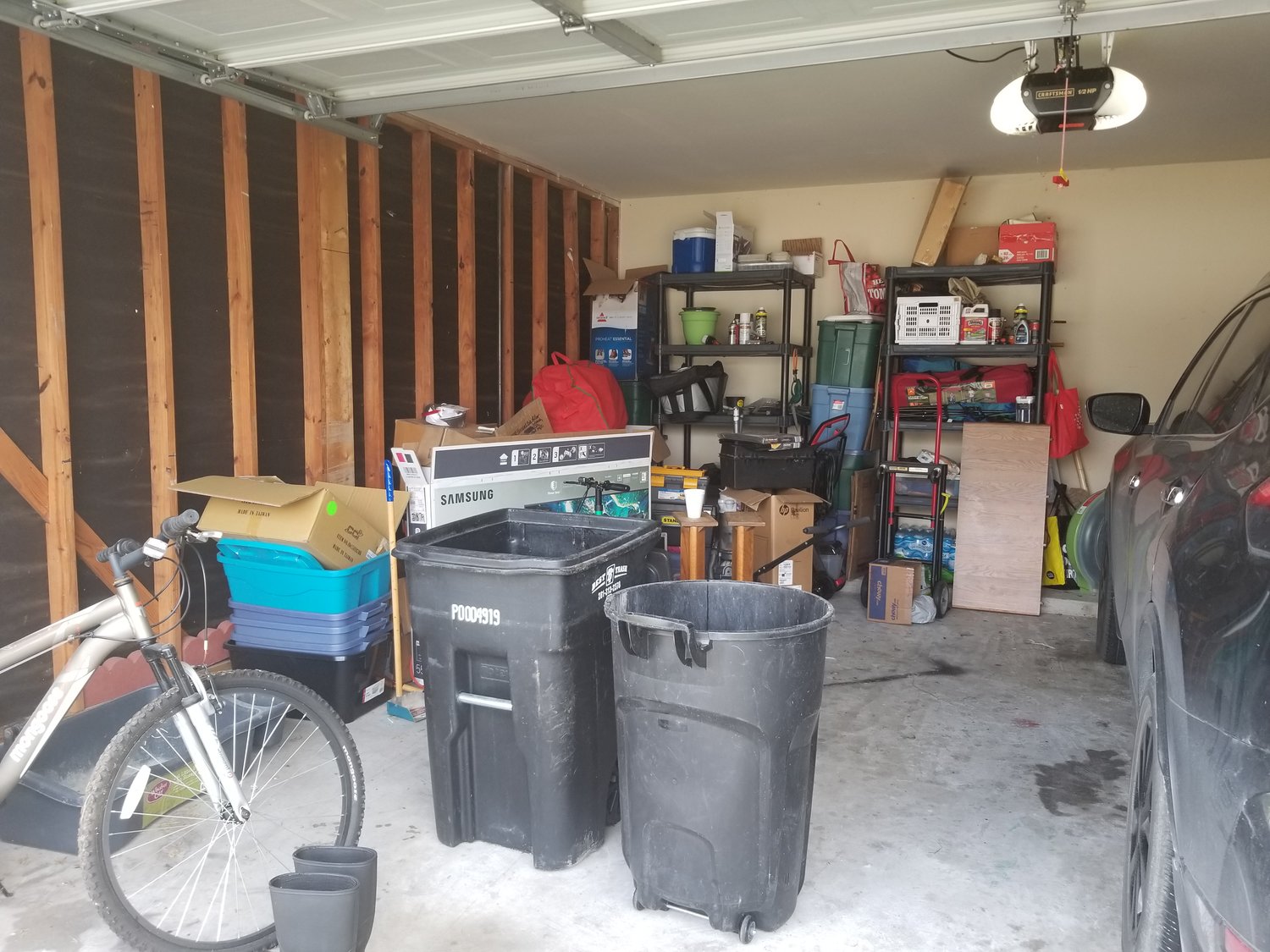
Source
There are many options when it comes to buying lumber. There are many different sizes, shapes or finishes that you can choose from. Rough sawn lumber for example is unfinished lumber that has not been sanded or finished and which has been cut into planks. This type of lumber tends to be stronger than other types because it carries extra moisture, but it is also thicker than surfaced wood. The following are some benefits of using rough sawn lumber for your woodworking projects.
Its availability and low cost are its main pros. Rough lumber can't be treated, and it isn't often sold at hardware stores. This type of lumber does have its advantages and disadvantages. Although it is less expensive per board foot, it is more expensive to transport. It takes longer to finish than treated wood. This is why you might consider it when deciding on how much lumber you want to purchase. If you are planning to use rough sawn lumber in your project, it is worth purchasing a large quantity and a smaller amount for finishing.
FAQ
Do I need to be a genius to succeed in woodworking?
No. No. Woodworking isn't rocket science. To create stunning works of art, anyone can learn to use basic power tools.
Is it difficult to start my woodworking business?
It is difficult to start your own woodworking company. There are many regulations and legal requirements that you will need to comply with. But, this doesn't mean you need to go through all of the trouble of setting up your business. Many people decide to join established businesses. You will only have to pay membership fees, taxes, and other charges.
How do I know what tools are best suited for me?
When shopping for tools, it helps to think about your needs and preferences. Do you prefer metal or plastic handles? What size nails and screws do you usually use? Would you rather use hand tools than power tools?
Where can I begin with woodworking
It is best to actually build furniture to learn how to make it. While you will need tools and make mistakes, you will eventually master the art of building furniture.
First, choose a project you would like to complete. You could make something as simple or complex as a box. Or you could build a whole entertainment center. After you have decided on a project to work on, contact a local woodworker that specializes in this type of work. Ask them for suggestions on the tools you will need and where to buy them. You might even ask whether there's someone else you can talk to who does this kind of work.
How can I organize my shop?
First, make sure you have a designated space for tools storage. Make sure your tools are clean and free of debris and dust so they can be used properly. Hang tools and accessories using pegboard hooks.
How much do hobbyists need to invest in starting a business?
If you're looking to start your own woodworking business, you'll probably need some capital to buy the necessary tools and supplies. Start by getting a small circular saw saw, drill press or circular saw. These items don't cost much so they won't break your budget.
Statistics
- If your lumber isn't as dry as you would like when you purchase it (over 22% in Glen Huey's opinion…probably over 10-15% in my opinion), then it's a good idea to let it acclimate to your workshop for a couple of weeks. (woodandshop.com)
- The U.S. Bureau of Labor Statistics (BLS) estimates that the number of jobs for woodworkers will decline by 4% between 2019 and 2029. (indeed.com)
- In 2014, there were just over 237,000 jobs for all woodworkers, with other wood product manufacturing employing 23 percent; wood kitchen cabinets and countertop manufacturing employing 21 percent. (theartcareerproject.com)
- Average lumber prices rose about 600 percent between April 2020 and May 2021. (familyhandyman.com)
External Links
How To
How to make wood joints
This tutorial will show you how to join two pieces of wood together. We'll use the "pocket hole joint," which means we drill holes in the wood and then glue them together. This method works great if your wood is straight and smooth. You may want to consider other methods, such as dowel joining. These are the steps
-
Drill Pocket Hole Joints. To start, measure and mark where you want to put the pocket hole joint. You will then drill 3/4" deep holes through each piece of wood with a jigsaw, handheld drilling machine, or hand-held drill.
-
Sand Smooth. Sanding the wood's edges will help ensure that the joint won't split later.
-
Glue Together Apply glue to both the ends of the wood. Let the wood sit for 5 minutes, then clamp it together.
-
Attach the Pieces together. After the glue has dried properly, clamp the pieces together to make sure they are flush.
-
Trim Joinery. After the glue dries completely, trim off any excess wood around the joint.
To be able to turn the pieces inside-out, leave enough room between them.