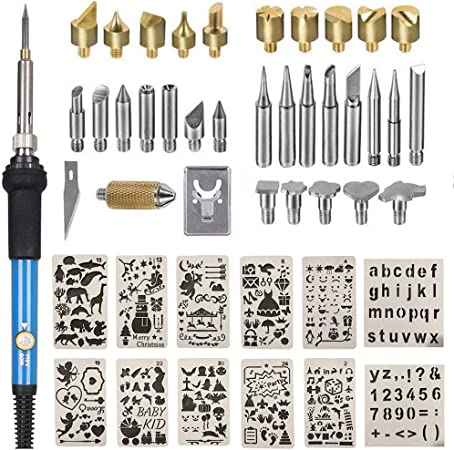
Once you have the right materials, it's now time to create your burning wood art. There are many different types of stencils that you can use, such as Lettering, Numbering or Mesh. It is also possible to use stencils for oil pencil designs. To get started, follow these simple instructions:
Lettering stencil
A lettering tool to burn wood is very beneficial. It can provide consistent dimensions and shapes. The lettering stencil is made from food-grade PET, or polyethylene terephthalate, which is safe for the body and is easy to clean. It is also safe for the user to avoid inhaling dangerous smoke and burns. It is essential to wear a safety mask and respirator before burning wood.
A pencil is a good option if you are unsure which stencil to choose. You should trace the design with a pencil onto the wood. If you don't, your stencil may melt. A good tip for creating an accurate lettering stencil for burning wood is to make sure to seal the wood, as this will help protect your artwork from further damage. A sharp knife tip or an open flame can be used to trace the design.
Numbering stencil
The numbering stencil is a useful tool for making decorative signs or labels. These stencils are made of food-grade PET, or polyethylene terephthalate, a type of plastic. This material is totally safe for human use, odorless, and can be re-used. It is lightweight, flexible, durable, and flexible. Additionally, it is nontoxic, making it an excellent choice for decorative signage. Lowe's has a wide selection of craft stencils.
These stencils are made out of PET material. They can be washed easily and are very flexible. They are also durable, and can be easily cleaned. The stencils come in a three-inch square and can be used over again. And because they are reusable, they can be used for many other DIY projects as well. You can use them for wedding showers, open houses and home decor. You can choose from a wide range of designs and shapes to match any occasion.
Mesh stencil
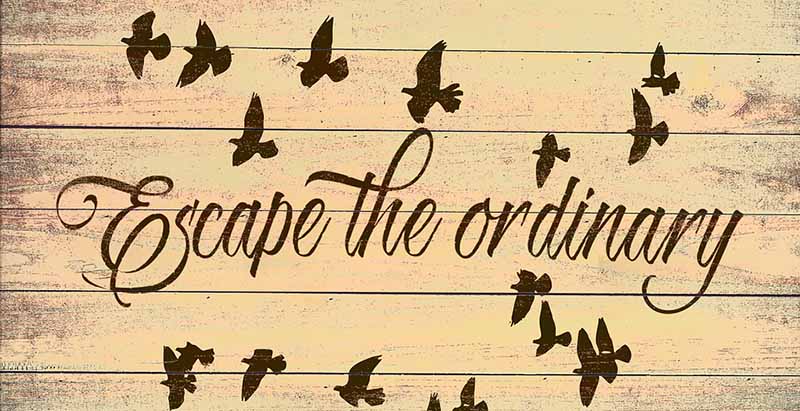
Mesh stencils can be used to create your own unique style of burning wood. These stencils are sold separately from Torch Paste. You'll need a medium strength brush and squeegee to create small designs. You'll also need a heat gun of at least 1000 watts. Finally, you'll need a substrate, such as wood or metal.
A set of freehand tracings or stencils can also be purchased. The first set of stencils you need will have a pattern. While the second set will have freehand patterns, they can be used to create your own stencils. You can also purchase a set of wood-burning tips, such as triangles or circles. A stand is also a must, as wood burning can be messy.
The stencils are printable or can be printed. You can also use a photo of an object to create a stencil. It is essential that the design you create matches the wood type. A piece of pine can be traced with a bird. This is a great method to use photographs in your woodworking projects.
Graphite stencil
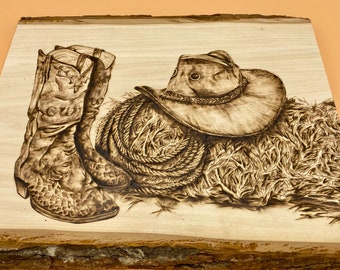
A graphite template is useful if you are looking to burn patterns or designs into wood. You can download free graphite stencil patterns online and use them to guide your flame while you burn the wood. To erase the design, you can use a damp cloth to remove the stencil. The stencil can be used on any wood that has not previously been burned. After the stencil is dry, you can color it using oil pencils. But, before you begin, make sure to have a graphite scavenger.
You will need to heat the transfer tip first before you can make a graphite-scanning stencil for burning wood. To transfer the design to wood, first heat the tip. This is an easy way to transfer the design to wood. However, it's best for beginners. A stencil is another option to make a design that will stick in the wood.
FAQ
Are you able to teach yourself woodworking
The best way to learn anything is by doing. Woodworking is an art form that requires patience, practice, skill, and experience. To master any craft, it takes time.
You can learn the most effective way to master a skill is by actually doing it. Start small and learn from your mistakes.
Do you know anything more about woodworking?
It is easy to underestimate how much work it takes to make furniture. Finding the right wood for the project is the hardest part. There are so many options for wood, it can be difficult choosing the right one.
Another problem is the fact that not all wood has the same properties. Some woods will crack or warp with time. Others will split or crack. These are important considerations to make before you purchase wood.
Do you have any suggestions for starting a woodworking shop?
It can be difficult to start a woodworking shop. If you are passionate about your hobby, it will not be difficult to put in the work. Plus, you'll probably enjoy the challenge of running your own business.
You should remember that unexpected issues may occur when you launch a new venture. Unexpectedly, money might run out. Maybe customers won't be willing to pay what you want. These situations are necessary for survival.
A good tip is to open a separate bank account for your business. You'll be able to track how much money comes in and out.
Do I need to be a genius to succeed in woodworking?
No. Woodworking is not difficult. It is possible to learn basic tools and techniques that will allow you to create beautiful art.
Statistics
- Overall employment of woodworkers is projected to grow 8 percent from 2020 to 2030, about as fast as the average for all occupations. (bls.gov)
- Most woodworkers agree that lumber moisture needs to be under 10% for building furniture. (woodandshop.com)
- Woodworkers on the lower end of that spectrum, the bottom 10% to be exact, make roughly $24,000 a year, while the top 10% makes $108,000. (zippia.com)
- In 2014, there were just over 237,000 jobs for all woodworkers, with other wood product manufacturing employing 23 percent; wood kitchen cabinets and countertop manufacturing employing 21 percent. (theartcareerproject.com)
External Links
How To
How to make wood joints
This tutorial will demonstrate how to join two pieces together of wood. We will use the "pockethole joint," which means that we drill holes in the wooden pieces and then glue them together. This method works great if your wood is straight and smooth. Try dowel joinery instead if your wood doesn't look straight. These are the steps
-
Drill Pocket Hole Joints. Measure and mark the location where you would like to place the pocket hole joint. Then drill 3/4 inch deep holes into the ends of each piece of wood using a jig saw or handheld drilling machine.
-
Sand Smooth. The wood's edges can be sanded to prevent splitting.
-
Glue both sides together. Apply glue to both the ends of the wood. Allow it to cool for at least 5 minutes before you attach the pieces.
-
Connect the pieces. After the glue has dried you can attach the pieces to form a flush joint.
-
Trim Joinery. Trimming the joinery after glue has completely dried.
Make sure to leave enough room between the pieces so that you can turn them inside and out.